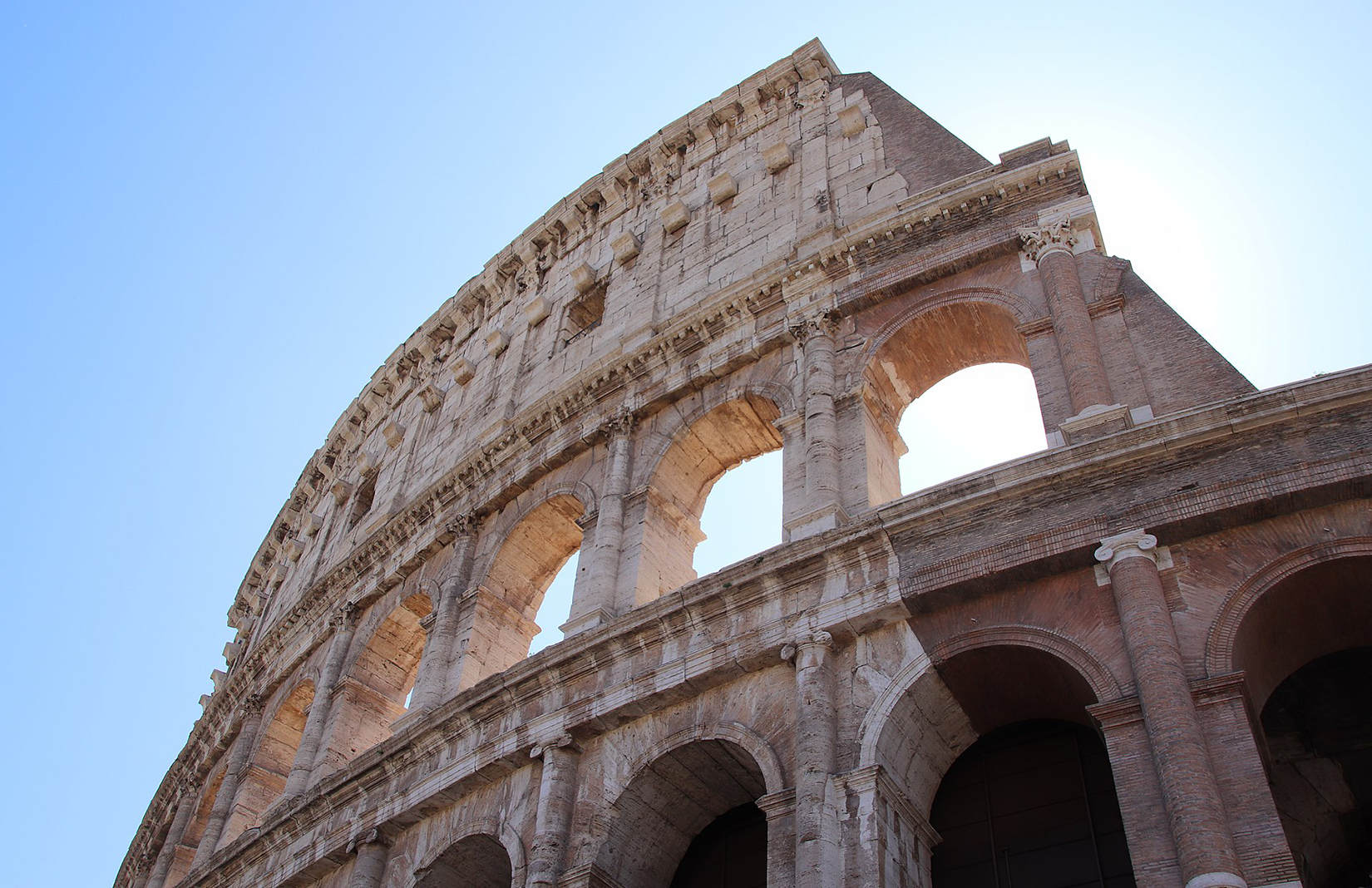
Photography: Gary Todd / CC BY 2.0
The Romans’ most enduring legacy is arguably their architectural one, with landmarks such as the Coliseum and Pantheon and ancient aqueducts standing strong for over 2,000 years. But until now, the durability of Roman concrete – which has endured for millennia while modern concrete can disintegrate in decades – was believed to be due to volcanic ash and slaked lime.
Researchers from MIT and Harvard in the US, and DMAT and the IMMS in Italy and Switzerland analysed a sample of 2,000-year-old concrete taken from a wall at Privernum in central Italy that was typical of Roman concrete used across the empire. The unexpected key to the ancient recipe? Omnipresent, tiny white chunks of stone called lime clasts.
‘Ever since I first began working with ancient Roman concrete, I’ve always been fascinated by these features,’ explains Admir Masic, author of the study and associate professor of civil and environmental engineering at the Massachusetts Institute of Technology. ‘These [lime clasts] are not found in modern concrete formulations, so why are they present in these ancient materials?’
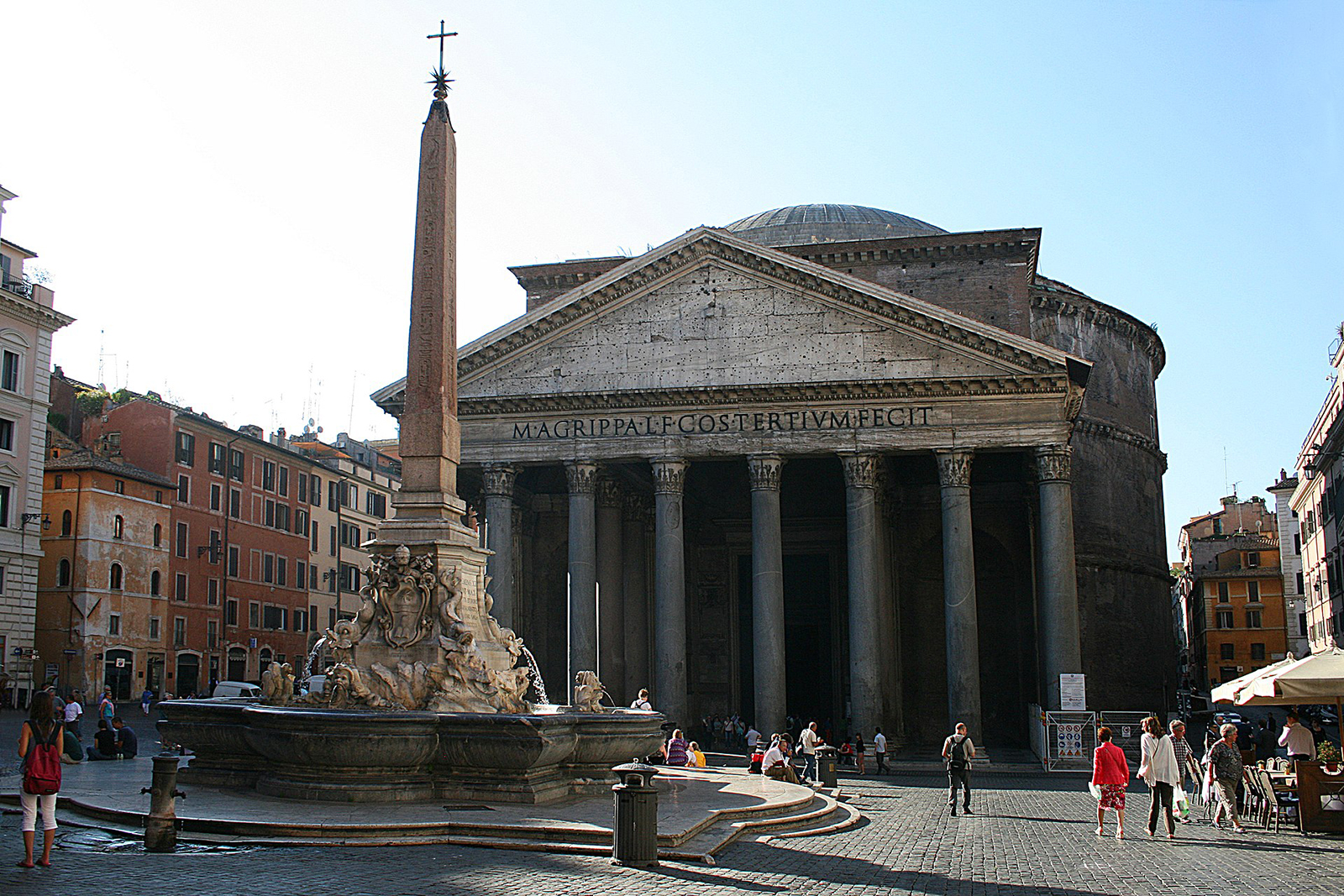
Researchers initially thought the Romans used slaked lime as the binding agent for concrete, as suggested by contemporary texts, and assumed the presence of lime clasts was merely the result of ‘sloppy mixing practices’. However, they realised the lime clasts actually pointed to the use of quicklime – calcium oxide, the most reactive, dry form of limestone – as the binding agent of choice.
They also discovered the lime clasts ‘self-heal’ cracks created by weathering by dissolving into fractures and recrystallising with exposure to water to ‘heal’ the surface.
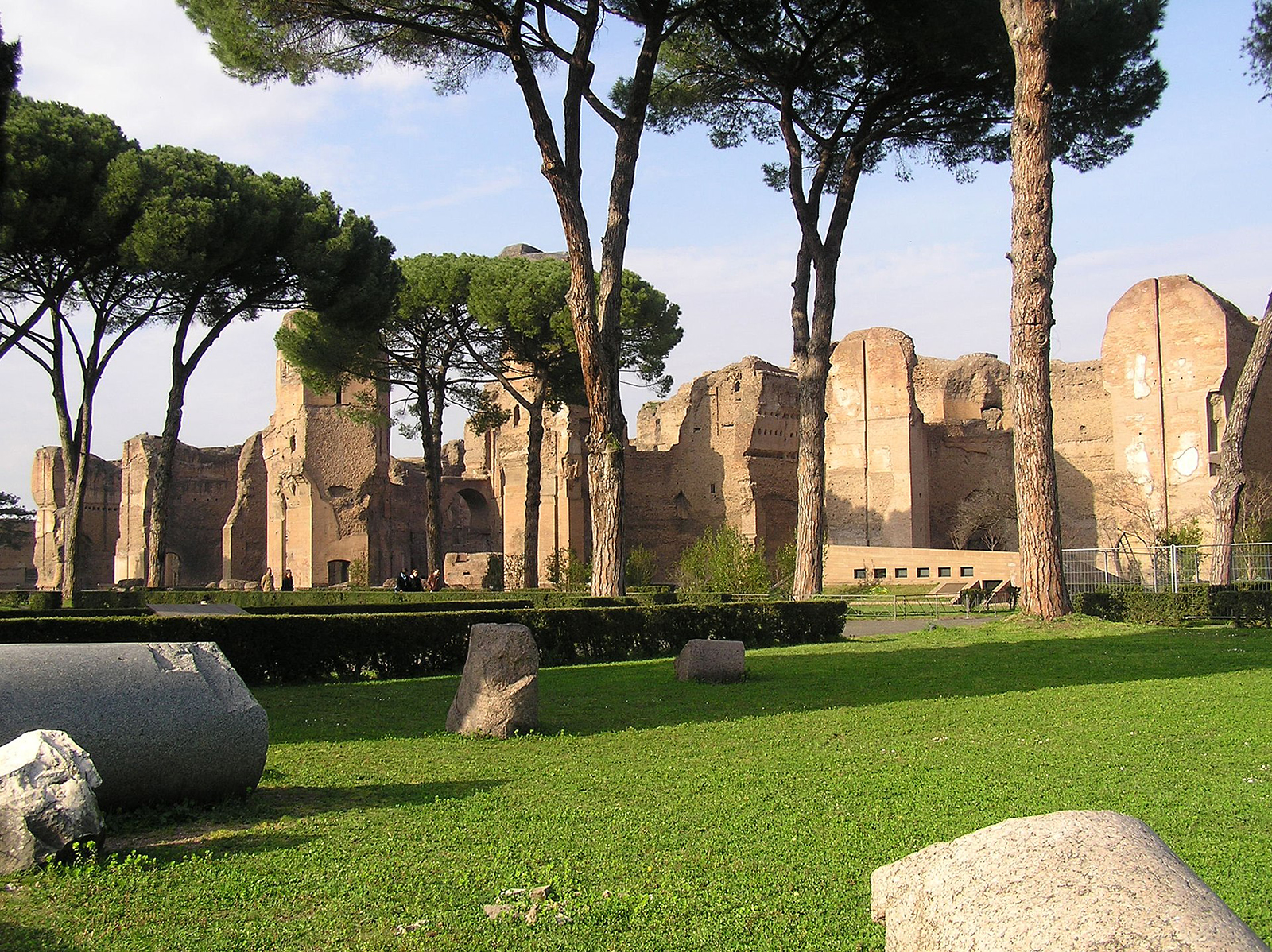
Researchers further concluded that lime clasts are formed at extreme temperatures, meaning Roman builders were ‘hot mixing’ to create their super-durable, quick-build concrete.
‘When the overall concrete is heated to high temperatures, it allows chemistries that are not possible if you only used slaked lime, producing high-temperature-associated compounds that would not otherwise form. Second, this increased temperature significantly reduces curing and setting times since all the reactions are accelerated, allowing for much faster construction.’
The findings offer potential take-aways for modern builders too, as Masic concludes: ‘It’s exciting to think about how these more durable concrete formulations could expand not only the service life of these materials but also how it could improve the durability of 3D-printed concrete formulations.
Read the full findings, published in the journal Science Advances.